friction weld bend test|free bend test welding : commercial Another name for bend testing is transverse beam testing or flexure testing. This method measures how the material reacts after bending and increasing . See more 6 de jun. de 2022 · O ator participou do 'Domingão com Huck' neste domingo, 5, e recebeu uma declaração da filha mais velha, Giulia Lins. No recado, a jovem de 21 anos elogiou .
{plog:ftitle_list}
WEB12 de set. de 2023 · SÃO PAULO: Rafael; Rafinha, Alan Franco, Beraldo e Caio Paulista; Pablo Maia, Alisson, Rodrigo Nestor e Lucas Moura; Luciano e Calleri. Técnico: Dorival .
Strength testing is a large part of friction welding quality control because many OEMs have specifications to meet for the required strength to ensure maximum performance of the component. To validate optimal friction welding parameters and evaluate the durability of the welded materials, you use the bend test. Bend . See moreAfter welding the two materials from the friction welding process, remove a strap from the center of the cross sectioned metal from the welded portion. You need . See moreHowever, the bend test does not show a quantitative bond from the friction welding, but people associate this method with Tension testing – tensile, yield, and . See moreAnother name for bend testing is transverse beam testing or flexure testing. This method measures how the material reacts after bending and increasing . See more
AFW performs non-destructive weld testing with ultrasonic weld inspection and destructive weld testing, including bend, hardness, impact, tensile, and torque.
The bend test is a simple and inexpensive qualitative test that can be used to evaluate both the ductility and soundness of a material. It is often used as a quality control test for butt-welded joints, having the advantage of simplicity of .
Bend testing is the most commonly, economical and simple qualitative mechanical testing used to check the material ductility and soundness. The test is more commonly applied .
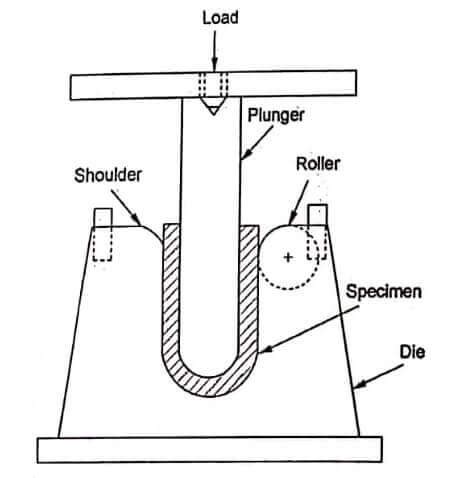
This bend test, of a shaft friction welded to a forged ring, demonstrates the incredible strength of the friction welding process. This heavy-wall tube bonded to a solid base gave way before the . A destructive bend test assesses a friction weld joint for mechanical integrity and bonding strength.
Combined with information and parameters gathered during friction welding, analysis and results can be built into a database to improve the lifecycle management of your product. Learn more about friction weld analysis and .A welded specimen is subjected to bending forces to determine its capacity to sustain deformation without fracture or failure. We provide a full explanation of the welding bend test in this post, .
Depending on the characteristics requiring inspection, we use various destructive test methods for friction welds: Bend Tests: free bend, guided bend, longitudinal bend, transverse bend. Etch Test. Hardness Tests: Brinell hardness, Rockwell .
The guided bend test on welds is designed primarily for metal plates and pipes and provides a quality control check that helps determine the ductility of the weld and the effectiveness of the welding process.Rotary Friction Welding creates a permanent bond between two (dis)similar pieces. This bond is typically as strong or more stronger than the individual pieces. There are various ways of testing the bond strength which includes .Guided Bend Tests apply to testing of weld ductility where controlled bending to a specific angle is part of the evaluation. Bend Testing Advantages Over Other Tests Bend tests tend to be more cost-effective than many other forms of .
During the bend test, the material containing the weld is supported on both ends by the test fixture, while a load is applied at its center point. Materials Testing System. For ASTM E290 testing we recommend using an Industrial Series . A destructive bend test is conducted on a stainless steel to carbon steel friction weld joint. American Friction Welding (AFW) is North America's largest sub.Inconel Weld Bend Test. Friction welding bend tests are common to assess mechanical integrity and bonding strength. This testing method involves subjecting a friction-welded specimen to bending forces, which simulate real-world conditions and evaluate the weld’s resistance to deformation. A predetermined load is applied gradually to the .
Friction & Wear Testing; Custom Solutions; Precision Measuring; Industries. Additive Manufacturing; . The bend test is a qualitative test that can be used to evaluate the safety of a material and its ability to withstand pressure without changing shape or rupturing. . The purpose is to ensure the weld has properly fused to the parent metal .Hastelloy Weld Bend Test. Friction welding bend tests are common to assess mechanical integrity and bonding strength. This testing method involves subjecting a friction-welded specimen to bending forces, which simulate real-world conditions and evaluate the weld’s resistance to deformation. A predetermined load is applied gradually to the . The study investigates the effectiveness of a novel joint configuration, the double-butt-lap (DBL), in friction stir welding (FSW) to join 6-mm-thick AA 6061-T6 plates. Four welds, including a simple square butt (SSB) configuration and three DBL variations (with UB to LB ratios of 1:2, 1:1, and 2:1), were executed. Using consistent parameters, the investigation evaluates .Nct Friction Welding is a privately held company in Colchester, CT was established in 1983. Over 75,000 welds annually, CNC machining, testing. 860-666-8424. Friction Welding; . induction/furnace temper/anneal, UT inspect, dye penetrate inspect and bend/tensile test – all in-house. Operating from its 8400 square foot facility located in .
SS to CS Weld Bend Test. Friction welding bend tests are common to assess welded joints’ mechanical integrity and bonding strength. This testing method involves subjecting a friction-welded specimen to bending forces, which simulate real-world conditions and evaluate the weld’s resistance to deformation. A predetermined load is applied .Download scientific diagram | Three point bend test on 25mm thick 6082 T6 aluminium alloy bobbin weld from publication: Friction Based Welding Technology for Aluminium | The friction processes . This study specifically investigates the inertia friction welding process of S355 bogie crosshead tubes, with the aim of improving the weld quality and achieving one-time formation of the crosshead tube and tube seat. . Bend Test. To investigate the ductility of inertia friction-welded joint, a three-point side bend test was carried out on .AWS B4.0:2016-AMD1 v Personnel (Amendment) AWS Committee on Mechanical Testing of Welds P. S. Lester, Chair AZZ WSI J. A. Grantham, Vice Chair Welding & Joining Management Group S. P. Hedrick, Secretary American Welding Society D. A. Fink The Lincoln Electric Company J. W. Sowards NIST Boulder L. Van Leaven Consultant R. F. Waite .
In the curve above, the upper yield point is denoted by Y u, the highest stress before sudden extension takes place, and its value is affected by surface finish, the shape of test piece, and rate of loading.. The lower yield point, which is normally measured in commercial testing, is denoted by Y L, the lowest stress producing the most elongation.Such large elongation of the . During the friction welding operations, the friction welding condition was set to the following combinations: a friction speed of 27.5 s −1 (1650 rpm), a friction pressure of 30 MPa, a range of friction times from 0.04 to 3.0 s, a range of forge pressures from 30 to 150 MPa, and a forge time of 6.0 s. To observe the joining phenomena during .
A destructive bend test assesses a friction weld joint for mechanical integrity and bonding strength.
Friction Stir Welding (FSW) is a solid-state joining technique, which was invented in The Welding Institute (TWI), United Kingdom in December 1991 and was first applied to aluminium alloys [2]. . Another reason is that it is due to incomplete penetration of tool pin on root side of weld. After the bend test, if there is no micro cracks . This paper presents metallurgical and mechanical properties of dissimilar metal welded joints between Nickel-base superalloys, viz., Inconel 718 and Nimonic 80A. The base metals were welded using electron-beam welding (EBW) and rotary friction welding (RFW) processes. Radiography test on both the weldments revealed no weld defects. The weld . For bend test, the load is increased until cracks start to appear on face or root of the weld for face and root bend test, respectively, and angle of bend at this stage is used as a measured of ductility of weld joints. The higher the bend angle (needed for crack initiation), greater is the ductility of the weld joint. Friction welding is a popular solid-state joining technique used in industries which require joining similar and dissimilar materials. . Three-point bend tests; Visual inspection; Optical microscopy; Scanning electron microscopy (SEM) . Learn more about friction weld analysis and understand more about the range of testing we offer. https .
Our testing capabilities: bend testing, metallography & material microstructure. Helium leak test, ultrasonic, dye penetrant and fluorescent penetrant. 860-666-8424. Friction Welding; Services. Friction Welding Services; CNC Machining; Metallurgical and Non-Destructive Testing; Supply Chain Management; About us; In the present work, the behaviour of an AA6061-T6 alloy joint through friction stir welding was studied comprehensively under a set of processing parameters so as to establish a better microstructure-strength relationship in the joint. In-depth investigations have been done on intermetallic compounds and their phases using SEM, XRD, optical microscopy, and EDS, and . In this work, friction welding process was attempted to join Ti to 304L SS. Direct friction welding of Ti to 304L SS results in a stronger weld in which failure occurs in the Ti base metal during tensile testing. However, the joints have almost zero bend ductility that has been attributed to the formation of intermetallics due to mechanical .
Operational and experimental setup 3.1 Sequence of operation Sequences of operation that indicates the friction welding are shown in figure 3.1. . Code Strength Deflection 1 S1000 8.4KN 25 2 S1200 8.8KN 25 3 Base metal 8.2KN 25 The above result confirms that weld specimens passes the bend test and allowing for very high bend angles and cracks . Friction Welding: Process, Types, and Advantages. Joining metal parts with friction and no external heat is what’s involved. Published: Aug 30, 2019 05:19 AM EST
Test materials used for friction weld trials and research. Cycle Time The total time required to complete a friction welding cycle on a machine. . (MTI) is a privately-held, fourth-generation company headquartered in South Bend, Indiana, specializing in transformational, custom-engineered friction welding and resistance welding solutions for .Abstract— Friction welding is an only till date known method to weld similar as well as dissimilar metals. . As-welded bend test samples failed with almost zero bend ductility. The bend ductility was improved to 5° PWHT (Post weld heat treatment). .
Indian Mahogany moisture meter
webJonas Oliver - O Escolhido cifra. Aprenda a tocar essa música usando as cifras, tablaturas e versão simplificada com o Cifras.
friction weld bend test|free bend test welding